数字工厂解决方案将IT和OT的深度融合,以数字化思维重构制造业业务模式和流程,有效解决制造业企业核心痛点,全面赋能生产制造全流程,提高工厂的整体效率和质量保证。数字工厂解决方案利用信息系统、物联网、边缘计算、大数据、人工智能和云计算等先进技术把工业研供产销全链路联接,客户全业务场景透明化,实现自动采集、数据分析、可预测、闭环管理的新型制造。
数字工厂及数字孪生正处于快速发展期,技术体系不断完善,产业融合持续提速,行业应用加速渗透,未来,随着先进制造技术等的不断发展,数字孪生将进一步在数据采集、建模、可视化等多个方面提升产业应用价值。
-
计划、生产、运营无法协同
整体数字化程度不高、生产过程不透明、业务环节难协同、缺乏精细化管理,面对生产异常问题无法快速反应与流程追溯。
-
缺乏数据整合治理
无法精准掌握设备管理数据、产品品质数据、能源能耗数据等,无法形成数据闭环式融合。
-
生产计划不合理
计划时间节点难以精确编制,排程不合理,经常出现订单延误、漏排情况,且对异常信息的反馈处理能力较弱。
-
质量检验内容繁杂,工作效率低
首检、巡检、工序检验、终检等检验结果无法及时反馈分析。主要依靠纸质记录,出现质量问题追溯效率低。
-
现场异常响应、处理不及时
无法实时收集及分析现场生产数据,没有建立异常生产处理机制,经常出现人力资源和物料的浪费。
-
工艺管理经验主义
工艺工序缺乏可视化管理,因工艺变更而出现差错。
基于核心产品智造业务平台及数字孪生平台,构建了涵盖工业物联、生产管理、质量管理、数据分析治理等主要功能的数字工厂解决方案,帮助离散型、混合型生产企业有效优化企业的生产管理模式。强化生产过程中的管理和控制,实现生产全链路数字化管理,助力企业加速实现工业4.0转型。
无纸化应用 | 搭建基于整个企业的无纸化管理平台,包括生产质量管理、车间管理、设备管理、移动应用、生产看板等,实现从人工操作向无纸化转变的过程。达成整体企业数字化、生产过程精准透明、业务环节协同、企业精细化管理。
数据可视化应用 | 基于物联网、边缘计算技术,将生产设备、流水线、工控系统等生产环节的数据进行实时采集,通过时序数据库或其他数据库进行存储,再通过BI等可视化分析软件进行实时展示分析,形成数据应用的落地和闭环。
全场景物联应用 | 面向工业现场复杂多样的装备,通过自研工业物联网网关OctoGateway, 利用物联网技术,通过有线、Wifi、5G等方式,将工厂核心生产区域、复杂多样的设备、仪器智能工具等进行数据采集与接入,形成人、生产、产品、管理可追溯、可控制的全流程管理模式。
在统一平台上集成质量控制、文档管理、生产调度等方式,从而实现生产过程的计划、生产、工艺、质量、设备管理及预警。
为企业实现生产过程的透明化管理、生产过程的异常信息监控,生产过程的质量管控及数据的共享、准确和实时奠定基础。
改善生产过程中的人为统计和纸质数据记录工作,提高人工绩效,降低生产周期,提升数据完整性。
利用孪生平台的建模能力,对工厂、车间、产线以及关键设备逐级建模,并进行结构化的3D可视化呈现,通过实时数据协议,将采集到的制造现场关键生产要素数据,如人员数据、机器数据、物料数据、规则数据、环境数据,实时传输到工厂虚拟孪生体中,从而建立物理体与虚拟孪生体之间的实时互动和精准映射。
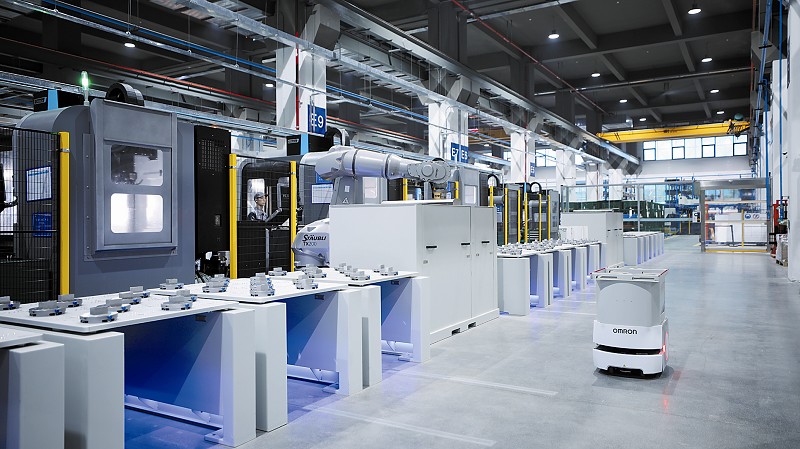
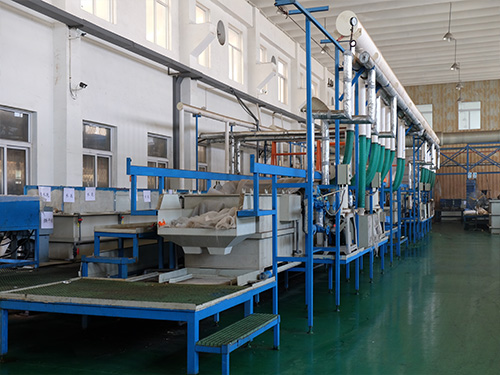